Power surges are commonly blamed when controls go bad on high-end units. I am not sure how often this is an accurate diagnosis versus how often this is just an easy scapegoat for unexplained parts failures. Plus … let us all be honest for a minute and acknowledge that as technicians we have all been guilty of condemning a control board because the system was operating abnormally and we did not understand what was happening … so therefore it must be that fancy looking control board.
While I am skeptical of how often a power surge is blamed for an “unexplained” component failure, the fact remains that power quality is a concern on modern HVAC equipment that did not exist as often on older generation HVAC equipment. Think about it, we have replaced electromechanical relays for printed circuit boards with relays and switches built on. These newer components create better control options for our equipment and allow us to improve the operating efficiency … but they are also more sensitive to being damaged than older relays with heavier contacts built into the switches. This issue compounds once we start getting into the realm of changing frequency to operate motors at the highest efficiency.
While many people would equate lightning to being the most frequent cause of power surges, another common cause can be electrical grid switching. Electrical utilities when operating power generating equipment will operate that equipment at constant speeds to keep the efficiency high.
As demand for the power they are creating fluctuates they will adjust where the power is allocated rather than adjusting the speed of the power generating equipment. When the power is being switched from one grid to another, power disturbances can occur, this is where spikes can often occur. These transient voltage spikes are generally very short lasting, often measured in microseconds (one microsecond being equal to one millionth of a second).
It is during these instances where damage can be caused to electronics. Surge Protectors … or possibly better described as Surge Suppressors … are a cost-effective way to protect valuable components from transient voltage spikes. These devices will often be installed at the specific product they are protecting. The installation places the device in parallel with the equipment and the surge protector will attempt to absorb and shunt voltage spikes to prevent them from reaching the protected equipment.
How do surge protectors work? Commonly, surge protectors will contain a component called an MOV (Metal Oxide Varistor). This component is designed to absorb excess voltage and give it a controlled path to ground. An MOV has three parts: a piece of metal oxide material in the middle, joined to the power and grounding line by two semiconductors. These semiconductors have a resistance that varies dependent on voltage. When the voltage is correct, an MOV does nothing. If the voltage spikes, then the resistance through the MOV will decrease and the MOV can conduct a lot of current to eliminate the excess voltage. Response time for MOV’s is generally in the nanosecond range (one nanosecond being equal to one billionth of a second). Another form of surge protection that is being used by some manufacturers is a gas discharge tube. This concept is like an MOV, but the difference is in using an inert gas instead of a metal oxide varistor. The gas is what separates the two semiconductors and under normal operating conditions the gas has a very high resistance. However, under a spike in voltage the gas will become ionized and the resistance will reduce allowing for a controlled shunt to ground.
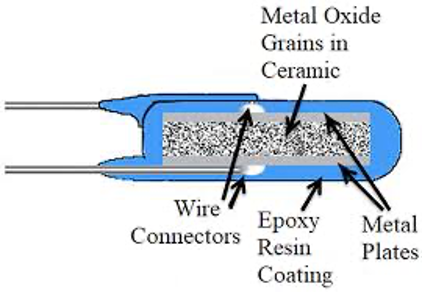
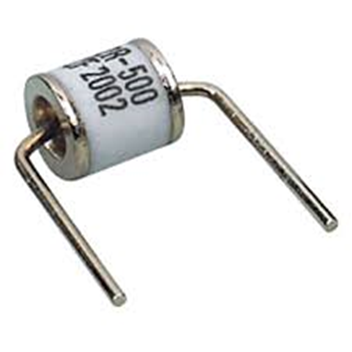
It is important to be aware that there are limitations to these devices and that proper installation is key. Both Metal Oxide Varistors as well as Gas Discharge Tubes have limited life expectancy. As these components are regularly used, they will begin to breakdown and become less effective. Eventually they will no longer function as intended at which time the surge suppressor should be removed and replaced. Many of these devices do have indicator lights on them that will stop working once the MOV or GDT has reached the end of its life. This is a great feature to visualize the time to replace the surge suppressor. Replacement of these devices should be viewed as a preventative maintenance item and I would consider there need of replacement to be a good sign … since that would indicate they were needed for protection. A final consideration should be given to ensuring proper installation of a surge protector. Most times the devices will be installed at the service disconnect for the equipment being protected. This is the area where an improper installation is commonly done. Many installers will simply double tap the surge protector wires with the line voltage feeding the equipment. This is almost always a violation of National Electrical Code 110.14(A). Placing two conductors underneath one terminal lug (referred to as “double tapping”) is not permitted unless the lug is specifically marked for more than a single connection. It is crucial, from a liability standpoint to ensure these devices are connected properly. Recently, a line of surge protectors has been released by Rectorseal that includes a disconnect box. These products are already inclusive a specially designed connectors to ensure installations are done according to National Electric Code. They are available in a 30-amp fused, 60-amp fused, and 60-amp non-fused configurations. To my knowledge they are the first company to resolve this potential installation issue.